Electron Gun: Difference between revisions
Line 132: | Line 132: | ||
====Lathe Machine: Drilling==== | ====Lathe Machine: Drilling==== | ||
The three components of the Einzel lens, anode, and | The three components of the Einzel lens, anode, and Wehnelt cylinder were sculpted out from a 42mm by 350mm (diameter/length) aluminum rod with the use of a lathe (a machine that rotates a workpiece about an axis of rotation to perform an operation such as cutting, sanding, drilling, etc.). After securely clamping down the aluminum rod, the rotational gears were set to “low” with a rotational speed of 105/610 rounds per minute (RPM) based on drill bit size: (Large/Small), and a drill bit secured within the “Tail Stock”. | ||
<br /> | <br /> | ||
Line 151: | Line 151: | ||
</ul></div> | </ul></div> | ||
Other than the manufactured items mentioned above, | Other than the manufactured items mentioned above, the filament was also prepared. The glass of the bulb was broken by lightly tapping the bulb with a metal hammer in a plastic bag. Broken glass fragments are then disposed of, resulting in the following: | ||
[[File:Filament.jpeg|300px|thumb|none|Broken bulb with exposed filament]] | [[File:Filament.jpeg|300px|thumb|none|Broken bulb with exposed filament]] |
Revision as of 16:28, 29 April 2022
Electron Guns have been used since the late 1940s in cathode ray tube (CRT) televisions and monitors.
The design of our electron gun can be understood through its two separate functions: electron emission and electron acceleration. Namely, to first introduce electrons into the system and then to accelerate these electrons, in a controlled manner, towards a target.
The introduction of electrons is done through thermionic emission. An electric current is passed through a filament which will then undergo Joule Heating. Thermionic emission will take place once the filament is sufficiently heated. This introduces electrons into the system.
The acceleration is achieved by differentially biasing electrodes within the electron gun to create an electric field that will accelerate the electrons towards the target in a controlled manner. The last clause requires more than mere potential differences but electrostatic lenses such that the electron beam can be coaxed into a desired trajectory. Broadly, both these objectives are achieved by having an acceleration section followed by a focusing section.
Directly following Thermionic emission, the electrons are subject to an accelerating potential. This accelerating potential is provided by an electrode (termed the anode) which is held at a positive potential difference from the filament. This causes electrons emitted from the filament to be accelerated towards the plate. Working in tandem with the anode is the Wenhelt Cylinder. Once accelerated past the anode, the beam is focused, again, with an Einzel lens.
These two, loosely defined, steps should result in an electron beam that is focused on a target. The target could be anything from a screen coated in phosphorous (to show the beam spot) to a Faraday Cup which can then be connected to a current measurement device.
Team Members
Aliki Sofia Rotelli (A0236272H)
Lai Tian Hao (A0236351L)
Lim En Liang, Irvin (A0173028J)
Tan Chuan Jie (A0154805E)
Idea
There are two parts to this project. The first would be to create the electron source which seems to be done with the use of a Lenard/Crookes tube [1]. Secondly, we would want to focus this electron beam into a spot with the use of a homemade magnetic lens (probably a solenoid of some form). We could perhaps perform a measurement of the focal length with respect to the magnetic field strength of the lens.
Concepts
Focusing Lens
Beam Resolution
One of the most important considerations scaling down is the Rayleigh criteria. The Rayleigh criteria relates the critical dimension (CD), or smallest feasible feature size resolvable by an optical system, to the imaging wavelength (𝜆) and numerical aperture (NA). This criteria is crucial. As a result of decreasing the critical dimension.
The Wehnelt cylinder
The Wehnhelt cylinder is a negatively biased cylinder located right after the filament. It influences the focusing of the electron beam and the electron emission from the filament. When tuned appropriately, the Wenhelt Cylinder, together with the anode, aids in the emission of electrons from the filament by creating a net electric field from the attractive (to the electrons) anode and repulsive Wehnelt. Being negatively biased, the Wehnelt cylinder also acts as a convergent electrostatic lens which focuses the electron beam path from the filament to the anode.
Einzel Lens
Like the Wehnelt Cylinder, the Einzel lens is also an electrostatic lens. In this electron gun, the Einzel lens is made of three cylindrical tubes in series along the direction of the electron beam. Due to the electrostatic symmetry, the ions do not lose energy through the focusing process. In operation only the middle Einzel is actively biased (positively). The other components of the lens being held at ground potential.
Schematic of Electron gun
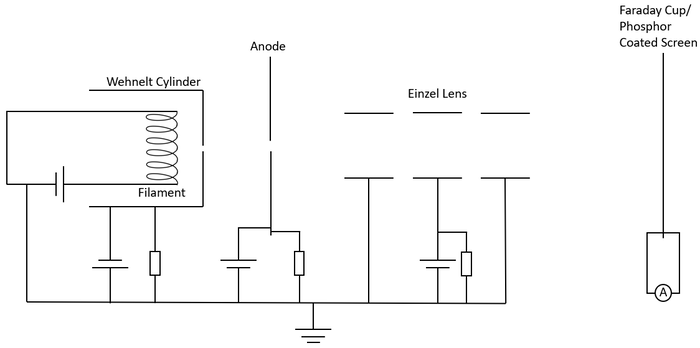
Simulated Proof of Concept
Simulations were performed in SIMION based on a proposed arrangement of the components mentioned above.
With parameters:
- Wehnelt: -200V
- Anode: 1000V
- Middle Einzel: 500V
-
A Simulation of the focused electron beam with Wehnelt cylinder and Einzel lens (Top-Down Cross-Sectional View) -
A Simulation of the focused electron beam with Wehnelt cylinder and Einzel lens (Isometric View) -
A Simulation of the focused electron beam with Wehnelt cylinder and Einzel lens (Potential Field)
Design of the electron gun's "central column"
Based on the schematic of the simulation, the development of a "central column" was designed using SOLIDWORKS, which consists of:
- Acrylic plate
- Einzel lens
- Anode
- Wehnelt cylinder
Acrylic Plate
The acrylic plate was created in a disk shape with a 100mm outside diameter and a 28mm inner diameter. In addition, the disk's inner ring features a 1mm by 32mm (depth/diameter) recessed on both sides. The recessed was created to allow for the secure installation of subsequent elements.
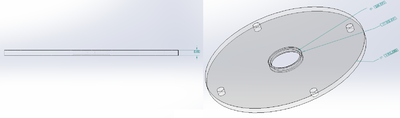
Einzel lens
The three components of the Einzel was designed with dimensions:
- Outer diameter: 32mm
- Inner diameter: 28mm
- Length: 30mm
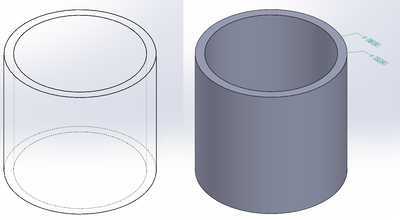
Anode
The anode was designed with dimensions:
- Outer diameter: 32mm
- Apeture (diameter): 8mm
- Thickness: 2mm
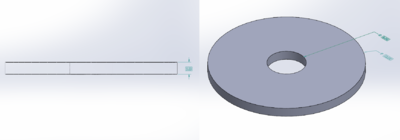
Wehnelt cylinder
- Outer diameter: 32mm
- Inner diameter: 28mm
- Apeture (diameter): 8mm
- Length: 30mm
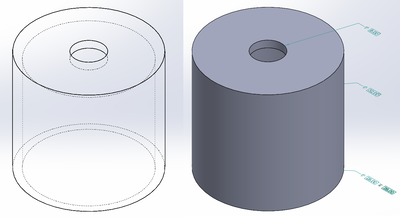
"Central column" design
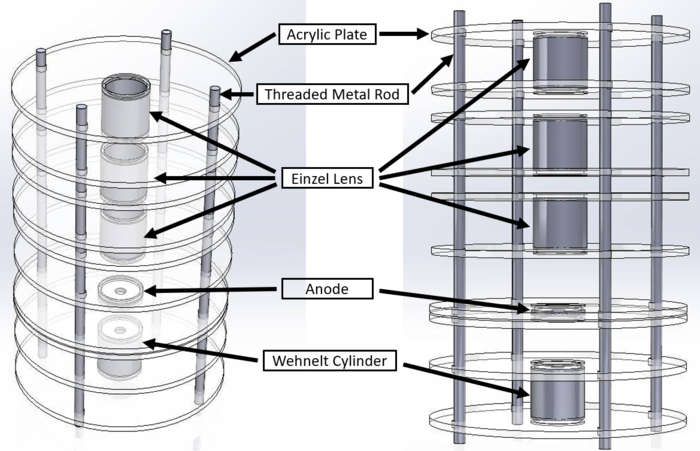
Central column with chamber design
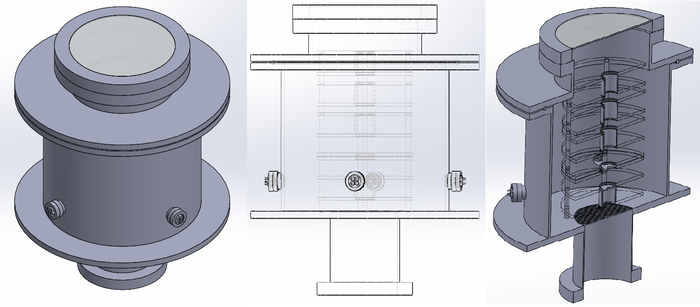
Equipment & Components
The following items were considered for the system:
High Vacuum (HV) Components
- Roughing Pump
- Turbo-Molecular Pump
Electrical Components
- High Voltage Power Supply Unit (PSU) (up to 5kV)
- Current Controlled PSU
Beam Focusing Components
- Einzel Lens
Measurement Components
- High Vacuum Digital Gauge, with range ~ mbars
- Edwards PRM10 (Pirani Gauge)
- Edwards D145-41-000 (Penning Gauge)
Other Components
- Filament (Possible choices)
- Tungsten (W) (Used in our system)
- Lanthanum Hexaboride (LaB6)
- Cerium Hexaboride (CeB6)
- Phosphors
- Zinc sulfide(ZnS) (Copper/Silver Activated)
- CF-40 Copper Gaskets
Setup
Manufacturing of central column
All of the items listed below were made in the workshop.
Acrylic Plate
The laser cutter is unable to make cuts at varying heights. To work around the laser cutter's limitations, a different approach was devised. First, a disk was cut out of a 5mm thick acrylic sheet with an outer radius of 100mm and an inner diameter of 32mm. Second, a 32mm/28mm (outer/inner) diameter ring was cut. Following that, the pieces were put together with an adhesive compound that allowed for a 1mm recess on both sides of the disk.
[Insert photo of acrylic plate]
Nine additional disks were manufactured in the same manner to obtain a total of ten disk plates.
Lathe Machine: Drilling
The three components of the Einzel lens, anode, and Wehnelt cylinder were sculpted out from a 42mm by 350mm (diameter/length) aluminum rod with the use of a lathe (a machine that rotates a workpiece about an axis of rotation to perform an operation such as cutting, sanding, drilling, etc.). After securely clamping down the aluminum rod, the rotational gears were set to “low” with a rotational speed of 105/610 rounds per minute (RPM) based on drill bit size: (Large/Small), and a drill bit secured within the “Tail Stock”.
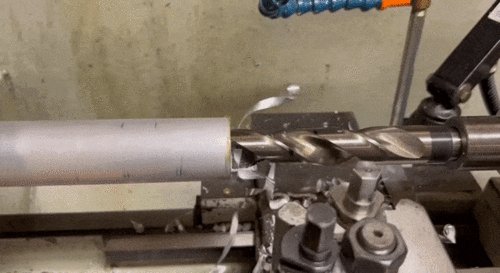
Lathe Machine: "Facing"
After achieving the structure's inner diameter, a "facing" tool was used to remove the surface material from the outside construction, "thinning" it from 42mm to 32mm. Rotational gear was set to low-610 RPM when "facing."
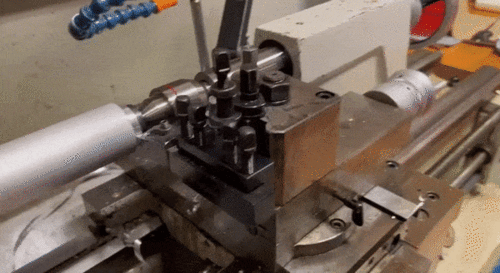
Manufactured items
The following items were manufactured for the system.
Other than the manufactured items mentioned above, the filament was also prepared. The glass of the bulb was broken by lightly tapping the bulb with a metal hammer in a plastic bag. Broken glass fragments are then disposed of, resulting in the following:
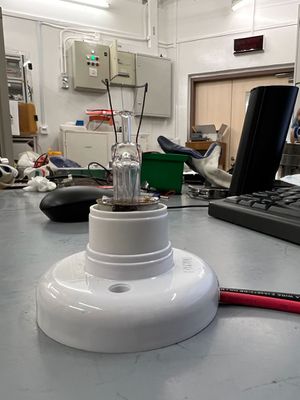
Chamber Setup
Note: While setup the external ports of the chamber as well as assembling the centre column, latex gloves were worn during this process.
- M5 nuts were utilized as a locking mechanism to guarantee that acrylic plates were firmly secured in place (Top and bottom of the acrylic plates).
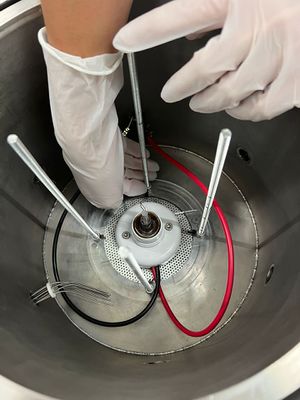
- The wehnelt cylinder was then carefully lowed into the chamber to ensure no contact between it and the filament.
- The rest of the component which includes: the anode and three einzel lens were then assembled within the chamber to achieve a full stack similar to the illustration of the schematic diagram.
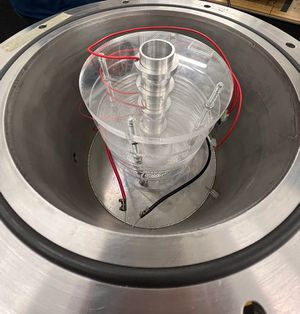
- With the central column setup completed, the phosphor was then mounted on the chamber lid with the use of Kapton tape. (Note: During the process of mounting, glass slide shattered causing a slight misalignment of the phosphor with respect to the center of the column.)
Fully Assembled System
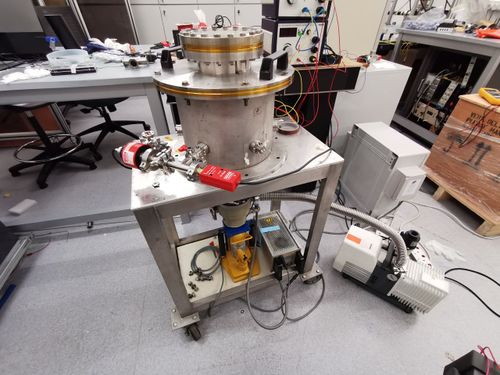
Measurements/Test
Phosphor Characterization
The phosphor powder used in this project was kindly provided by Nejilock. The composition is >99% zinc sulfide. We characterized the powder using a fluorescent microscope. The powder is excited with UV light and the emission is collected. The spectrum of wavelengths emitted is presented in the figure below. The majority of the emission is in the 450-550 nm region, meaning the powder will have a blue/green glow.
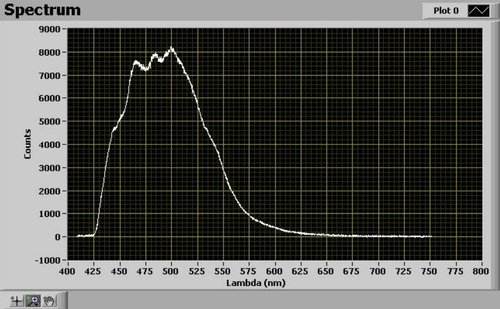
Pressure Characterization
The roughing pump and the turbomolecular pump were both characterized while they were connected to the chamber. Do note that for a turbo-roughing system, vacuum pressure criteria of approximately mbar must first be achieved using the roughing pump before the turbomolecular pump can be turned on. This is to ensure that the turbines blades of the turbo remain undamaged. Maximum vacuum pressure achieved with this setup is mbar after 16 hours and mbar after 48hours of pump down. With an initial maximum of mbar at 41mins.
Conductance Test
After all of the components were assembled, conductance tests of individual components were performed to ensure proper connections between the components and the feedthroughs.
Experiment/Results
Similar to the parameters simulated:
- The wehnelt cylinder at potential: -200V
- Anode and the first and third Einzel lens at the potential: 1kV
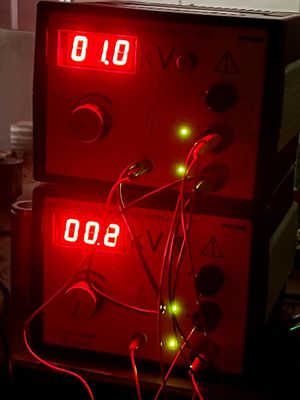
- Filament power supply:
- Voltage: 10V
- Current: 0.1104A
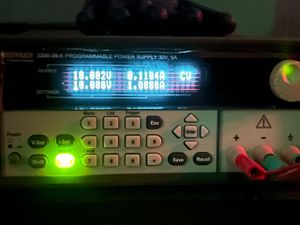
A tinge of fluorescence can be spotted which is illuminated from the phosphor coating. With a more prominent glow located at the top right quadrant of the phosphor coating. This coincides with the slight misalignment of the glass slides during installation.
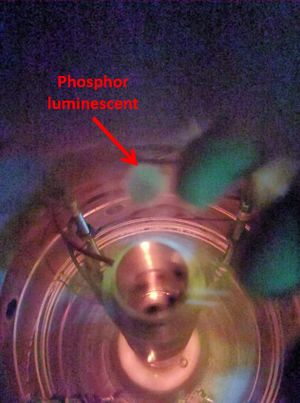